Is Your Equipment Malfunctioning or Is It Just Operator Error? Identifying the Real Problem
In the intricate world of technology and machinery, the line between user error and genuine operational problems can often blur, leading to confusion and frustration. This phenomenon, known as operator error, is a term that typically describes mistakes made by users due to misunderstanding or misusing equipment. However, there exists a myriad of issues that can masquerade as operator error, complicating troubleshooting processes and hindering effective solutions. Understanding these potential pitfalls is crucial for both users and technicians alike, as it can save time, resources, and even enhance safety in various operational environments.
One common issue that may be mistaken for operator error is equipment malfunction due to wear and tear. As machines age, their components can degrade, leading to performance issues that might initially appear to be the result of user mishandling. Similarly, software glitches or bugs can create scenarios where the system behaves unexpectedly, prompting users to question their own actions rather than recognizing the underlying technical fault. These situations highlight the importance of thorough diagnostics and a keen understanding of machine behavior.
Additionally, environmental factors can also contribute to confusion surrounding operator error. Changes in temperature, humidity, or even electrical supply can affect how equipment operates, potentially leading to errors that users might attribute to their own actions. By recognizing these external influences, organizations can
Common Issues Confused with Operator Error
Operator error, often attributed to human mistakes during the use of equipment or systems, can sometimes be misdiagnosed. Various underlying problems may lead to symptoms that resemble operator error. Understanding these issues is crucial for effective troubleshooting and resolution.
One such issue is software malfunction. When software does not perform as intended, it can lead to outputs or behaviors that seem to stem from user error. Common signs include:
- Unexpected crashes or freezes
- Error messages that are unclear or misleading
- Features that do not respond as designed
Similarly, hardware failure can present as operator error. Equipment that is malfunctioning or has not been properly maintained may produce results that appear to be the result of user negligence. Indicators include:
- Unusual noises from machinery
- Components that fail to engage or disengage
- Visible wear or damage to parts
Another contributing factor is environmental conditions. External factors such as temperature, humidity, or interference can impact equipment performance. For instance:
- High temperatures may cause overheating, leading to shutdowns
- Excessive dust or moisture can disrupt electronic systems
- Interference from other devices can lead to erratic behavior
Identifying the Root Cause
To differentiate between true operator error and these underlying issues, a systematic approach should be employed. Here are key steps to follow:
- Review Operational Procedures: Ensure that all users are following the prescribed protocols.
- Conduct Equipment Diagnostics: Utilize built-in diagnostic tools to check for malfunctions.
- Analyze Environmental Factors: Monitor conditions around the equipment to identify potential external influences.
- Gather User Feedback: Collect insights from operators about their experiences and any anomalies they have noticed.
Issue Type | Symptoms | Potential Solutions |
---|---|---|
Software Malfunction | Error messages, crashes | Update software, reinstall |
Hardware Failure | Unusual noises, failure to operate | Inspect and replace parts |
Environmental Conditions | Overheating, erratic behavior | Improve ventilation, relocate equipment |
By addressing these areas, organizations can significantly reduce the incidence of misdiagnosed operator errors. This not only enhances operational efficiency but also increases user confidence in the systems being utilized.
Common Problems Confused with Operator Error
Operator errors can often be mistakenly attributed to various underlying issues, leading to misdiagnosis and ineffective solutions. Recognizing these problems is essential for accurate troubleshooting.
Equipment Malfunction
Equipment malfunction is a primary issue that can be confused with operator error. Several factors contribute to this misattribution:
- Mechanical Failures: Broken or worn-out parts can lead to performance issues.
- Electrical Problems: Faulty wiring or power supply issues can disrupt functionality.
- Software Bugs: Glitches in software can result in unexpected behavior.
Symptoms of Equipment Malfunction | Possible Operator Error Confusion |
---|---|
Unresponsive controls | Misunderstanding of control functions |
Inconsistent output | Incorrect settings applied by the operator |
Frequent error messages | Operator misinterpretation of error codes |
Environmental Factors
Environmental conditions can significantly affect equipment performance, often leading to confusion with operator error:
- Temperature Fluctuations: Extreme temperatures may cause devices to behave erratically.
- Humidity Levels: Excess moisture can lead to electrical shorts or corrosion.
- Vibration and Shock: External vibrations can disrupt sensitive equipment.
Training Deficiencies
Inadequate training can lead to operator mistakes, yet these errors may stem from larger systemic issues:
- Lack of Familiarity: Operators may not fully understand equipment or software functionalities.
- Insufficient Instruction: Poor training materials can leave operators uncertain about procedures.
- High Turnover Rates: Frequent staff changes may result in inexperienced operators.
Systemic Issues in Workflow
Workflow processes can introduce challenges that appear as operator errors:
- Poor Communication: Lack of clear communication between team members can lead to misunderstandings.
- Inadequate Procedures: Ambiguous or poorly defined protocols can create confusion.
- Resource Constraints: Limited access to necessary tools or information can hinder performance.
Human Factors and Cognitive Load
Human factors play a crucial role in operational performance, and cognitive load can lead to errors mistaken for operator incompetence:
- Mental Fatigue: Operators may make mistakes when fatigued, leading to misinterpretation of tasks.
- Stress Levels: High-stress environments can impair decision-making abilities.
- Multitasking: Juggling multiple tasks can overwhelm operators, leading to errors.
Conclusion on Error Attribution
Recognizing the distinction between true operator errors and these common problems is vital for effective troubleshooting. Proper training, improved communication, and a focus on environmental and systemic factors can aid in reducing the occurrence of errors that are misidentified as operator mistakes.
Understanding Common Misinterpretations in Operational Errors
Dr. Emily Carter (Human Factors Specialist, Ergonomics International). “Many operational errors are mistakenly attributed to user incompetence when, in fact, they stem from poor system design. It is essential to analyze the context in which the error occurred, as environmental factors often play a significant role.”
James Thompson (Manufacturing Process Engineer, Precision Solutions Inc.). “Operators frequently face issues that appear to be errors on their part but are actually the result of equipment malfunctions or software glitches. A thorough investigation into the machinery’s performance is crucial to distinguish between true operator error and system failure.”
Linda Garcia (Quality Assurance Manager, TechSafe Industries). “In many cases, training deficiencies are misidentified as operator errors. It is vital to ensure that employees receive comprehensive training that addresses potential pitfalls in the system, thereby reducing the likelihood of confusion and mistakes.”
Frequently Asked Questions (FAQs)
What types of problems are commonly confused with operator error?
Technical malfunctions, software bugs, and hardware failures are often mistaken for operator error. These issues can arise from system updates, compatibility problems, or equipment wear and tear.
How can one distinguish between operator error and a genuine technical issue?
To differentiate, one should conduct a thorough investigation. This includes reviewing error logs, replicating the issue under controlled conditions, and consulting technical support documentation.
What signs indicate that an issue may not be operator error?
Indicators include consistent errors across multiple users, problems occurring after software updates, and issues that persist despite following proper operational procedures.
Are there specific troubleshooting steps to identify operator error?
Yes, troubleshooting steps include verifying user input, checking for adherence to operational guidelines, and conducting tests to isolate the problem to a specific component or process.
Can training deficiencies contribute to problems that appear as operator error?
Absolutely. Inadequate training can lead to misunderstandings of system functionalities, which may result in incorrect usage that mimics operator error.
What resources are available for resolving issues that may be confused with operator error?
Resources include technical support teams, user manuals, online forums, and troubleshooting guides provided by the manufacturer or software developer.
In the realm of operational processes, distinguishing between genuine problems and operator error is crucial for effective troubleshooting and resolution. Operator error often refers to mistakes made by individuals while using equipment or systems, which can stem from a lack of training, misunderstanding of procedures, or simple oversight. However, there are numerous other issues that may present similarly, leading to confusion and misdiagnosis. These can include equipment malfunctions, software bugs, environmental factors, and systemic flaws within operational protocols.
It is essential to adopt a systematic approach when investigating incidents that appear to be operator errors. By thoroughly analyzing the context and conditions surrounding the event, one can identify whether the issue is indeed due to human error or if it is a symptom of a larger, underlying problem. This process often involves gathering data, consulting with personnel, and reviewing operational guidelines to ensure a comprehensive understanding of the situation.
Key takeaways from this discussion emphasize the importance of proper training and clear communication within operational environments. Organizations should invest in ongoing education and support for their personnel to minimize the likelihood of operator errors. Additionally, implementing robust maintenance and monitoring systems can help detect and address potential equipment or procedural issues before they escalate into significant problems. Ultimately, a proactive approach to identifying and resolving issues will
Author Profile
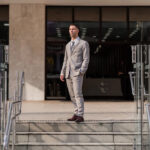
-
Jeremy Mazur is a statistician, researcher, and entrepreneur dedicated to bridging the gap between data science and real-world innovation. With a Ph.D. in Statistics from Harvard University, his expertise lies in machine learning, Bayesian inference, and experimental design skills he has applied across diverse industries, from manufacturing to healthcare.
Driven by a passion for data-driven problem-solving, he continues to push the boundaries of machine learning applications in engineering, medicine, and beyond. Whether optimizing 3D printing workflows or advancing biostatistical research, Jeremy Mazur remains committed to leveraging data science for meaningful impact.
Latest entries
- April 13, 2025Kubernetes ManagementDo I Really Need Kubernetes for My Application: A Comprehensive Guide?
- April 13, 2025Kubernetes ManagementHow Can You Effectively Restart a Kubernetes Pod?
- April 13, 2025Kubernetes ManagementHow Can You Install Calico in Kubernetes: A Step-by-Step Guide?
- April 13, 2025TroubleshootingHow Can You Fix a CrashLoopBackOff in Your Kubernetes Pod?